For decades, industrial-grade air curtains were used successfully for shipping doorways and interior applications where medium- and low-temperature environments required separation for energy savings, manufacturing quality control, or employee comfort. Various models for other building types have appeared over the last decade due to myriad innovations from manufacturers. These new types of air curtains are a direct response to requests for new applications ranging from:
- drive-thru windows for quick-serve restaurants;
- esthetic in-ceiling mount units for commercial building lobbies;
- spark-proof versions for hazardous industrial locations;
- walk-in cooler doorways in foodservice; and
- entrances to car washes.
Washing cars
In the last 20 years, air curtains have steadily progressed past basic industrial applications to help building owners fight various indoor air quality (IAQ) and energy battles. One case in point is a Québec car wash with a daily wintertime quest of battling Canadian roadway salt, dirt, and grime on vehicles. Saint Thomas-based, 80-site Le Groupe Harnois and its petroleum marketing organization found air curtains particularly effective in reducing energy and maintenance-intensive ice accumulations at its automatic car wash in Saint Charles-Borromee.
Sub-freezing weather typically required continual daily maintenance of removing ice from mechanical equipment due to the barrage of spraying and rinsing. Consequently, the overhead door’s rails and rollers, plus the mechanical car-washing equipment, regularly had ice buildups that needed routine removal and maintenance. The facility was built with gas-fired space heaters, but with a perpetually open 3 x 3-m (10 x 10-ft) doorway, energy losses were expensive and heating did little to offset ice accumulation.
Typical conventional air curtains are not built for these sorts of wet environments—in this case, the owner worked directly with a Montréal-based manufacturer representative to custom-design the product for car wash conditions. The company specified options of a stainless steel cabinet and three special hermetically sealed, waterproof 1/2-hp motors for the 3.4-m (132-in.) long unit’s three blowers. An on-board hot water coil that supplements the 46.5-m2 (500-sf) space’s heating was employed. The car wash’s existing boilers—which furnish hot water for washing sequences—also supply the air curtain’s on-board 173-MBtu/h hot-water coil.

The air curtain was installed by Joliette, Que.-based Enterprise de Refrigeration & Climatisation Claude Bédard. It is mounted above and inside the door opening, and manually calibrated to discharge air a few inches outside the door’s threshold to create a ‘seal’ that retains up to 80 per cent of the conditioned indoor air, while also preventing the infiltration of subfreezing outdoor air and wind bursts of 8 km/h (5 mph) or less. A thermostat in the facility’s mechanical room with an outdoor sensor activates the air curtain when outdoor temperatures approach freezing levels.
Longer-length curtains for cows
Until recently, 3.7-m (12-ft) long air curtains were the maximum length for a catalogued single construction unit. Wider doorways required custom-manufactured air curtains. Some manufacturers simply bolted together multiple modular units to cover a wide span. However, up to 4.9-m (16-ft) long air curtains are now general catalogue items for some manufacturers, which greatly reduces the cost.
Unlike multiple units bolted together, these single units typically do not need intermediate support, which can drastically cut installation time. Further, while the space between bolted units often creates air voids, single-construction products can employ blower and nozzle airstream widths that cover the entire span without any interruption or turbulence. The proper volume, velocity, and uniformity (VVU) of the airstream is critical to air curtain performance and efficacy.
For example, the Calgary location of a trucking company, Coastal Pacific Xpress, needed 4.9-m long air curtains in a tractor and trailer wash stall to keep equipment from wintertime freeze-ups. Additional costs associated with tandem units would have been otherwise prohibitive.
Longer air curtains have also piqued the interest of commercial farmers. Griesen’s Family Dairy located in Prairie du Sac, Wis., recently installed air curtains to curb production losses. The medium-sized 680-cow farm suffered winter production delays from automatic milking equipment freeze-ups located nearest the milking parlour entrances, and potential injury issues from slippery floors and poor indoor air comfort for employees and animals.
On ambient temperature days above 0 C (32 F), the floor’s radiant system supplied by a 400,000-Btu, stainless steel, 95.1-per cent efficient boiler combined with each cow’s inherent 4000-BTU/hr heat output, adequately maintains the milking parlor’s target temperature range of 3.3 to 4.4 C (38 to 40 F). The heating system was adequate despite the fact co-owner Hans Griesen prefers the two 4.9 x 2.4-m (16 x 8-ft) entryways to remain open through three daily shifts for the 24-stall herringbone-style milking parlor’s optimal productivity and animal ingress and egress. However, on subfreezing days, the heating system could not maintain set-point temperatures near the entryways.
Griesen first tried portable forced-air heaters. While the entrances were warmer, the $100/day fuel cost, combustion emission odours, and potential fire hazard were undesirable. Further, an employee dedicated to operating the two doorways all day was considered cost-prohibitive.
Griesen also considered both strip curtains and air curtain technology so the entry doors could stay open. Strip curtains are clear polyvinyl strips that hang loosely in a doorway to block air infi ltration and allow pedestrian passage. These were deemed too obstructive to the animals; further, his first review of an air curtain at a nearby farm was not positive.
In that other facility, an inexpensive air curtain was used, with short lengths bolted in tandem to span the wide doorway. The air curtain was noisy, its modular construction vibrated, and it failed to provide the proper VVU balance of air stream to prevent outdoor air infi ltration, according to Griesen.
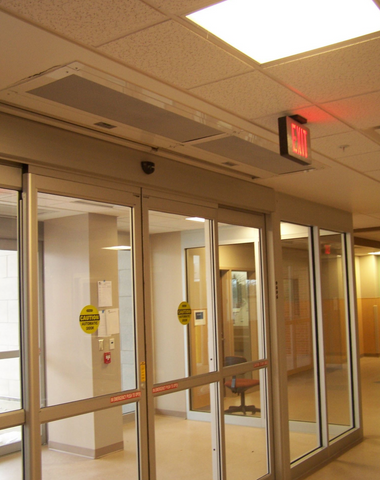
Clyde Conger, general manager for materials-handlin gequipment dealer Bernie’s Equipment Co. (Holmen, Wis.) recommended air curtains to retain heat in the milking parlour. Conger worked with a manufacturer’s engineers to specify two 4.9-m (16-ft) long, one-piece construction air curtains, which were then mounted above the space’s open doorways. The result retained up to 80 per cent of the facility’s energy even during wind loads of up to 8 km/h (5 mph). The air curtains had:
- corrosion-resistant, powder-coated finish;
- five high-efficiency 1⁄2-hp motors; and
- welded aluminized steel frame that retains a strong structural integrity in spanning across the wide opening.
Consequently, there are no gaps in the 216-m3/min (7631-cfm), 498-m/min (1635-fpm) air stream generated across the 4.9-m wide entryways, and the milking parlour equipment no longer freezes.1
Industrial safety
For years, doorways in hazardous industrial environments either needed custom-designed air curtains or were left unprotected from exposure to energy loss. The former is expensive and might surpass many industrial maintenance budgets, but now some air curtain manufacturers have catalogued hazardous location (HL) equipment, which reduces the price and also allows for a quicker availability.
In food-processing or pharmaceutical manufacturing industries, unprotected shipping doors are not an option because flying insects create sanitation issues. Meanwhile, chemical facilities and natural gas (CNG) bus garages have HL considerations such as fumes or airborne flammable dust that can easily ignite from electrical arcing.
Consequently, HL air curtains are constructed with explosion-proof motors and spark-resistant fans, electrical components, and materials. The air curtains also comply with electrical codes that dictate special requirements for HL sites.
Since industrial doorways can be expansive, modular or single-construction HL units must be able to cover the standard 4.9-m (16-ft) wide doorway and offer a range of motors from 1/2- to 15-hp, which is important for covering doorway heights as high as 6.1 m (20 ft). Optional steam and hot-water coils for heating between 54 and 82 C (130 and 180 F) to provide temperature rises that vary between 17 and 25 C (30 and 45 F), depending on the model, can also be added.
The metals used in air curtain construction are equally important as the components. For example, there should be no contact between ferrous metals for spark prevention.
Besides separating the environments at doorways, the continuous draw of air into an air curtain may add a ventilation benefit of helping minimize the formation of vapour air pockets.

Raising the esthetics with in-ceiling mounts
In the lobbies of hotels, hospitals, and other commercial spaces where esthetics are paramount, a visible metal box above a doorway, even when outfitted with high-technology powder coating and attractive grilles, have deterred some architects and engineers from specifying them. Therefore, newer in-ceiling mount air curtains with components recessed into the ceiling and a powder-coated flush-mounted frame have become popular.
In Laval, Que.’s Salle André Mathieu Theatre, the College of Montorency’s popular theatre productions draw huge crowds that fill the lobby and create standing lines outside the entrance doors long before productions begin. Waiting patrons held entrance doors open, which allowed winter winds to infiltrate and chill the lobby area as well as the theatre seating area. The lobby’s in-ceiling electric heaters could not maintain comfortable temperatures under those adverse conditions.
To solve the energy loss and indoor air comfort challenges, consulting engineer, Marcel A. Provost, P.Eng. (principal at MLC Associés Experts Conseils) specified 1829-mm (72-in.) long air curtains for each of the entrance’s four 2.4 x 1.8-m (8 x 6-ft) doorways. The vestibule entrance to the lobby and the theatre seating entrance each have a pair of air curtains. Provost specified a more esthetic in-ceiling mounted design that is flush with the ceiling and appears only as a common air supply grille.
The air curtains are activated when their respective doors are opened; they automatically shut off with a 60-second time delay after the door closes, performing energy-saving environmental separation that saves the college thousands in annual heating costs. They also have thermostatically controlled 20-kW heating coils with modulating devices that only use their capacity when the lobby temperature drops 1.1 C (2 F) below the set point.
Temperature drops of less than 1.1 C will throttle the heating coil down by pulsing on and off at full capacity every 15 seconds, depending on outdoor temperatures. Additionally, the fan is designed to run longer after the heating coil is shut off to take advantage of the available heat while it cools. This monitoring and controlling strategy is a sophisticated departure from industrial air curtains, many of which have only simple manual on/off switches.
To ensure air curtain performance is accurate, the college’s maintenance staff was also trained by the manufacturer to monitor airflow performance, nozzle and vane angles, and three-speed fan settings. The air curtains, which were installed by Serge Chabot & Fils (Marieville, Que.), have been successful in saving the college approximately 30 per cent annually with a payback of approximately three years.
Foodservice innovations
One of the fastest-growing segments of the air curtain industry is the many different innovations for foodservice and restaurant operations. For decades, these products were typically used only on back entrances to eliminate flying insects and improve overall sanitation near the shipping areas and kitchen. Today, models handle specific duties in areas such as walk-in cooler entrances, drive-thru windows, and the front entrance. All three scenarios are energy-savers, but the latter two are instrumental in minimizing fly infiltration that can affect sanitation.
“We’ve had a growing market in air curtains for drive-thru windows and walk-in coolers mainly from the foodservice end-user,” said Bill Myles, the president of a Richmond Hill, Ont.-based manufacturer representative firm for various IAQ-related products. “Now, we’re seeing consulting engineers specify these two products because they’re realizing their benefits. Even though drive-thru windows and walk-in coolers are a small part of the total energy savings for a restaurant, those little things really add up when you combine them.”
Walk-in cooler air curtains have been proven to surpass the energy-saving potential of swinging hinged doors and strip curtains; further, they produce a quick payback of less than two years, depending on the amount of door cycles.
Donoghue & Pivirotto Enterprises, a Pennsylvania quick-serve restaurant franchisee that operates four Arby’s stores, performed its own testing to determine the potential of reducing walk-in cooler energy use. The franchisee conducted a two-week audited test on a 3 x 3.7-m (10 x 12-ft) walk-in cooler at a 307-m2 (3300-sf) restaurant. With help from its HVAC/R contractor, ICA Mechanical, the company oversaw the outfitting and comparison of the walk-in cooler entrance with an air curtain for one week and one week without.
The results proved the refrigeration circuit’s compressor ran 1.75 hours less during one week of operation—a 27 per cent reduction in compressor run-time and equipment wear-and-tear. The improvement resulted in nearly 100 fewer operating hours per year for an estimated annual savings of $447 and a 1.6-year payback. Restaurants with larger walk-in coolers and more door cycles and foot traffic will realize a greater savings and shorter paybacks.
While they are now predominantly appearing as options on new models from walk-in cooler manufacturers, several suppliers make retrofitting easy with a kit that includes an air curtain designed specifically for the unique size and configuration of walk-in coolers. Included in some kits are a pre-wired 24-V control/load centre in a small enclosure and a magnetic reed on/off door switch. Once 120-V power is extended to the area, the pre-wired kit can be installed in as little as 15 minutes with conventional tools and basic electric knowledge.
Besides walk-in coolers, another trend in the foodservice and restaurant industries is the new drive-thru window air curtains, which are being used for various purposes in some locations of restaurant chains such as some Ontario Tim Hortons and McDonald’s, and some Harvey’s locations in Alberta. They minimize flying insect and outdoor air infiltration, protect the indoor employee from idling vehicle fumes and cold, winter air.
Conclusion
As energy consumption and costs become more important, and as the focus on indoor environmental quality and comfort increases, air curtain manufacturers are continuing to develop new products that can be specified to accommodate many more industries.
By Stephen Benes